出荷業務とは、顧客からの注文に基づいて商品を準備し、最終的に顧客へ届けるために発送する一連のプロセスのことです。
具体的には、以下の流れで行われます。
- 受注処理
- 出荷指示
- 在庫引き当て処理
- ピッキング
- 検品
- 梱包
- 仕分け
- 発送
出荷業務では、正確かつ迅速な作業が求められます。
しかし、この工程でミスが生じると、誤発送や発送漏れの恐れがあります。
ミスを放置すれば、顧客満足度の低下やブランドイメージの毀損につながるだけでなく、返品や再出荷に伴うコストも増大します。
本記事では、出荷業務の基本から効率化のコツまで、わかりやすく解説します。
物流現場で使える実践的な手法も紹介していますので、ぜひご活用ください。
出荷業務について知りたい、出荷業務を改善したいとお考えの方は、ぜひ最後までお読みください。
出荷業務とは
出荷業務とは、顧客から注文を受けた商品を、倉庫から顧客に向けて発送する一連の業務のことです。スムーズな商品配送を実現するために重要なプロセスであり、物流全体の品質にも大きく影響します。
物流の5大機能は「輸送・保管・荷役・包装・流通加工」ですが、出荷業務はこれらすべてに関わるため、物流プロセスの中でも重要な役割を担います。
出荷業務は、以下の流れで行われます。
- 受注処理
- 出荷指示
- 在庫引き当て処理
- ピッキング
- 検品
- 梱包
- 仕分け
- 発送
これらの作業を正確かつ効率的に行うことで、正しい商品を適切なタイミングで届けられるため、顧客満足度の向上にもつながります。
なぜ出荷業務の効率化が求められているのか
EC市場の拡大と、それに伴う即日配送や時間指定といった顧客ニーズの多様化によって、出荷業務の作業負担が日に日に増しており、物流プロセスにおける出荷業務の効率化が求められています。
また、2024年問題に関連した働き方改革法案により、トラックドライバーの時間外労働の上限規制が適用されました。
その結果、長距離輸送の制約が強まったことも、集荷時間の変更によるスケジュールの見直しや出荷業務の効率化を後押しする要因となっています。
また、出荷業務の効率化は、コスト削減や顧客満足度の向上、生産性の向上、競争力の強化といった事業成果への寄与も期待できます。
このように多くの要因から、出荷業務の効率化は重要度の高い取り組みといえるでしょう。
出荷業務の基本的な手順
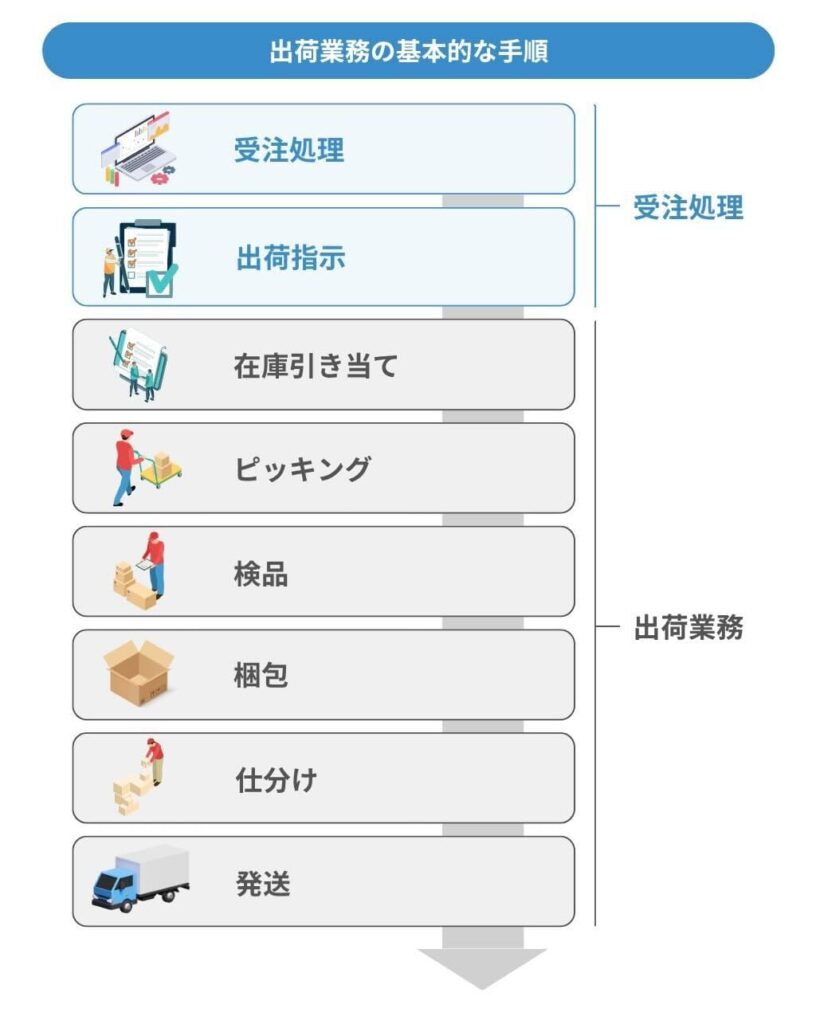
本章では、出荷業務の基本的な手順を解説します。
具体的な業務内容を見てみましょう。
1.受注処理
出荷業務の最初のステップとなるのが、顧客から注文を受ける「受注処理」です。
顧客からの注文を受け付け、受注データをシステムに取り込みます。
2.出荷指示
注文票や受注データを確認して出荷指示書を作成します。この指示書には、出荷する商品の種類、数量、配送先の情報、出荷日時などが含まれます。
3.在庫引き当て処理
出荷指示書に基づいて倉庫内の在庫を確認し、必要な商品を確保する「在庫引き当て処理」を行います。
引き当て処理とは受注した商品の在庫を確保し、その在庫を他の注文に使用されないようにする管理プロセスのことです。
在庫数から出荷予定の数を差し引くことで、在庫の上限数を明確にすることが目的です。
ただし、在庫引き当てはあくまでも在庫の確保を行う作業であり、この時点では商品のピッキングは行いません。
4.ピッキング
ピッキングとは、出荷指示書に従い倉庫内から注文の商品を取り出す作業です。
ピッキングには、以下の2種類の方式があります。
- 摘み取り方式(シングルピッキング方式)
- 種まき方式(トータルピッキング方式)
摘み取り方式(シングルピッキング方式)
摘み取り方式(シングルピッキング方式)とは、発送先ごとに商品を集めるピッキング方法です。
作業ミスが起こりにくく、シンプルな手順で実施可能です。ただし、注文数が多い場合は、作業員が移動する距離が長くなり、作業効率が低下する可能性があります。
摘み取り方式は注文ごとに必要な商品だけを効率よくピッキングできるため、多品種小ロットの商品を扱う場合や、ECサイトで個別注文が多い場合に適しています。
種まき方式(トータルピッキング方式)
種まき方式(トータルピッキング方式)は、複数の注文から必要な商品をまとめて取り出すピッキング方法です。一度に複数の注文を処理し、その後仕分け作業を実施します。
商品をまとめてピッキングするため、作業員の移動距離や作業時間が短縮され、効率的なピッキングが可能です。ただし、商品を集めた後に仕分け作業を行うため、十分な作業スペースが必要です。
種まき方式は、少ない種類の商品をまとめて出荷する場合に適しています。
5.検品
ピッキングが完了したら、出荷する商品に問題がないか検品を行います。
出荷前にしっかりと検品することで、不良品の流出を防ぎ、商品の品質を維持できます。検品は、目視や手作業で行うほか、バーコードやハンディスキャナを用いて数量や品番を確認し、在庫管理システムに記録する方法もあります。
【主な検品項目】
- 注文内容と納品内容が一致しているか(品番・数量・サイズなど)
- 商品に汚れ、傷、破損、不良がないか
- 商品ごとに必要な品質基準を満たしているか
検品の項目は商品によって異なります。例えば、アパレルの場合は糸のほつれ、縫製不良、寸法の不備などを重点的にチェックします。このように商品に適した検品項目を設定することが重要です。
6.梱包
検品で商品の状態に問題がなければ、梱包を行います。
梱包作業では商品が配送中に破損しないよう、商品の特性やサイズに合わせて段ボールや緩衝材などを選びます。
必要に応じて納品書や保証書などを同封し、取扱注意のラベルなどを貼付します。
梱包が完了したら、送り状を貼付し出荷準備が整います。
梱包時に用いられる緩衝材にはさまざまな種類があり、それぞれの特徴を理解して使い分けることで、より安全な配送につながります。
気泡緩衝材
気泡緩衝材とは、エアーキャップやエアーパッキン、エアークッションとも呼ばれる梱包材で、水濡れから商品を保護することが可能です。
割れ物、小物、精密機器などの梱包に適しています。
エアーピロー
エアーピローは、ポリ袋に空気を入れた緩衝材です。
耐久性やクッション性に優れており、箱と商品の隙間を埋めるために使用され、輸送中の衝撃から商品を守ります。
巻き段ボール
巻き段ボールとはエンボス加工紙とも呼ばれており、巻くことも、折り曲げることもでき、さまざまな形状の包装が可能です。
段ボールに入らない商品や不定形の商品の梱包に適しています。
その反面、クッション性に劣るため、衝撃に弱い商品の梱包には適していません。
紙パッキン
紙パッキンは、紙を細かく裁断した緩衝材です。
吸湿性があるため、湿度に弱い商品の梱包に適しています。
一方で、クッション性が低いため、破損の恐れがある商品の梱包には向いていません。
バラ緩衝材
バラ緩衝材は、コーンスターチやポリエチレンなどを主原料とした緩衝材で、粒状や円筒のような形状が特徴です。
小さな隙間や複雑な形状の隙間を埋めることができ、家電や精密機器など壊れやすい商品の梱包に適しています。
クラフト紙
クラフト紙は、新聞紙の原紙や古紙を原料にした紙製の緩衝材です。
丸めて隙間を埋める、商品を包むなど幅広い用途に対応可能です。
発泡スチロール
発泡スチロールは、軽さやクッション性があり、強度に優れた緩衝材です。
商品をしっかり固定できるため、電化製品のような衝撃に弱いものの梱包に適しています。
ただし、商品の形状に合わせて加工をする必要があり、コストがかかる場合があります。
ウレタンフォーム
ウレタンフォームはスポンジのような緩衝材で、クッション性に優れています。
電子機器や精密機器など傷から保護する必要がある商品の梱包に適しています。
ストレッチフィルム
ストレッチフィルムは、ラップのように密着力が高い緩衝材です。
商品を覆うことで荷崩れ、水濡れ、汚れを防止でき、段ボール板に固定するためにも使用されます。
ポリエチレンシート
ポリエチレンシートは、発泡ポリエチレンで作られた、薄いシート状の緩衝材です。
軽量で取り扱いやすく、水にも強いため湿気から商品を守ることが可能です。
断熱性にも優れており、温度管理が必要な商品や冷蔵品の梱包にも適しています。
7.仕分け
梱包が完了し送り状を貼付したら、配送先の企業や地域ごとに商品の仕分けを行います。
近年では、この仕分け作業の効率化を図るため、ソーティングロボットを導入する物流センターも増えています。例えば、ギークプラスでは、高精度な仕分けを可能にするソーティングロボットを提供しており、物流全体の最適化を実現しています。
高速かつ正確な仕分け能力を備えたソーティングロボットは、大量の荷物を迅速に処理することで、出荷時間の短縮に貢献します。
最大100kgまでの荷物を安全に扱えるため、軽量物から重量物まで幅広い商品に対応可能です。
ロボット本体は省スペース設計で、倉庫内の限られたスペースでも効率よく運用できるのが特徴です。
また、S20シリーズではフロアごとに小・中サイズの商品を効率的に仕分けられるため、ロボットの動作をモニタリングしながらタスクを調整することで、仕分け作業の最大効率を実現します。
ロボットとの連携により、自動搬送や無人での仕分けも実現できます。
複数階にわたる仕分けにも対応しており、倉庫の立体的な空間を有効活用できるでしょう。
梱包・仕分け・積み込みといった出荷前の工程を統合し、アウトバウンド業務全体の最適化と無人化を支援します。
8.発送
仕分けが完了した荷物を、配送先に向けて発送します。
社内の配送部門で発送を手配するか、提携している配送事業者に引き渡しましょう。
出荷業務で起こりうるミス
出荷業務では、以下のようなミスが起こるリスクがあります。
- 注文と異なる商品・個数を発送する
- 注文者と異なる住所に発送する
- 破損や汚損した商品を発送する
- 同梱物を入れ忘れて発送する
- 注文商品の出荷漏れが発生する
このようなミスがなぜ起こるのかその原因を、詳しく解説します。
注文と異なる商品・個数を発送してしまう
出荷の際に、注文と異なる個数・サイズ・カラーを発送する場合があります。
このような誤発送が起こるのは、以下の原因が考えられます。
- 出荷指示書の記載ミス
- ピッキング時の商品の取り違え
- 検品時のミス
色やサイズなどのバリエーションがある商品は、品番や管理番号を分けて管理することで、誤配送を防止することができます。検品時には、ダブルチェックを行い、誤発送のリスクを減らしましょう。
注文者と異なる住所に発送してしまう
手作業で送付状の記入や貼付を行う場合、送り状を他の荷物に貼付けて、注文者と異なる住所に発送するミスが発生しやすくなります。
発送先を誤ると、再配送が必要になるため余計なコストがかかるだけでなく、顧客に不信感を持たれる要因になります。
誤発送を防ぐには送り状を貼付する前に、注文時の配送先と一致しているかどうか、再確認する工程を設けることが必要です。
破損・汚損した商品を発送してしまう
検品が不十分だと、破損・汚損した商品を発送してしまうリスクが高まります。不良品の発送は、検品体制への不信感につながり、顧客からの信用の低下を招いてしまうでしょう。
また、取り扱う商品の種類が増えるにつれ、検品ミスが発生しやすくなる傾向です。ミスが起これば返品対応が必要になり、その分の作業量が増え物流の負担が大きくなるため、ミスを防ぐ体制づくりが欠かせません。
同梱物を入れ忘れたまま発送してしまう
納品書、伝票、保証書などの書類や、ノベルティなどを入れ忘れて発送するケースもあります。
たとえ商品自体に問題がなくても、必要な書類やノベルティグッズが同梱されていなければ、顧客の信用を損ねてしまう恐れがあるでしょう。
こうした同梱のミスを防ぐには、チェックリストを活用するなど倉庫内の管理体制を整えることが求められます。
注文商品の出荷漏れが発生してしまう
注文商品の出荷漏れは、注文情報の共有不足や在庫管理の不備が原因で発生することがあります。
例えば、複数の商品を一度に発送する際、特定の商品が梱包されず出荷されない、または作業中に商品が紛失するなど、出荷過程でのミスが出荷漏れを引き起こすことがあります。
出荷漏れは企業の価値を大きく低下させる要因になるため、作業フローの見直しが必要です。
出荷作業でミスが発生した場合のリスク
出荷作業でミスが起こると、さまざまなリスクが発生します。
- 顧客満足度やブランドの信用度が低下する
- 個人情報の漏えいに繋がる
- 無駄なコストが発生する
- 在庫データと実在庫に差異が生じる
出荷作業がもたらすリスクについて、詳しく解説します。
顧客満足度やブランドの信用度が低下する
出荷作業でミスが起こると、商品が予定通りに届かない、届いた商品を交換・返品しなければならないなど、顧客側に手間と時間がかかります。
これにより、顧客満足度やブランドの信用度が低下する可能性があります。信用が失墜すれば買い控えがおき、売上にも影響を及ぼします。
個人情報の漏えいに繋がる
宛先の誤配送や納品書の入れ違いにより、本来の注文者の個人情報が第三者に漏えいするリスクがあります。
誤って個人情報が送られた場合は、その情報が悪用される可能性もあるため注意が必要です。、加えて、状況によっては訴訟に発展し大きなトラブルとなるケースもあるため、長期的なブランドイメージにも悪影響を及ぼします。
無駄なコストが発生する
出荷作業で誤出荷が発生すると、返品や再発送の送料、さらには梱包作業などの費用がかかります。
また、作業員は再度商品を確認し、新たに発送手続きを行う必要があり、その分余計な労力がかかり人件費も増加するでしょう。
こうした対応に追われることで、本来の業務に支障をきたし、さらなる無駄なコストを生む原因にもなります。
在庫データと実在庫に差異が生じる
誤出荷が発生した場合、システム上の在庫と実在庫に差異が生じる可能性があります。
在庫に差異が生じた場合、ほかの顧客から注文を受けた際に在庫が足りず、注文のキャンセルや納期の延長が発生します。
また、実際の在庫数とシステム上の在庫数が一致しなくなり、その差異を補うために余分な在庫が発注され、過剰在庫が発生するリスクもあるでしょう。。
過剰在庫が発生すると、期限切れや需要の低下により販売価値が低下し、不良在庫を増やす原因になります。さらに、保管スペースを圧迫し、余分な保管コストや在庫管理の負担が増加します。
出荷業務のミスを防ぐ方法
出荷作業によるミスは、対策を講じれば防ぐことが可能です。
- ロボットにより倉庫の自動化を図る
- 倉庫内の環境を整える
- マニュアルを整備・更新する
- ダブルチェックを行う
- 作業員への教育やトレーニングを行う
- 受注管理システムを導入する
ここでは、出荷業務のミスを防ぐ具体的な方法を解説します。
ロボットにより倉庫の自動化を図る
ロボットを物流倉庫に導入することで、出荷作業におけるヒューマンエラーや人員不足を解消できます。
例えば、ピッキングや仕分け、商品の移動といった工程をロボットで自動化すれば、人手による作業に比べて処理スピードが大幅に向上します。さらに、作業ミスの削減や人件費の抑制といった効果も期待できます。
また、ロボットは24時間稼働可能が可能なため、人的リソースの制限を受けることなく、生産性の向上にもつながるでしょう。。
ここでは、ロボットによるピッキングサービスを提供する企業を3社ご紹介します。
ギークプラス
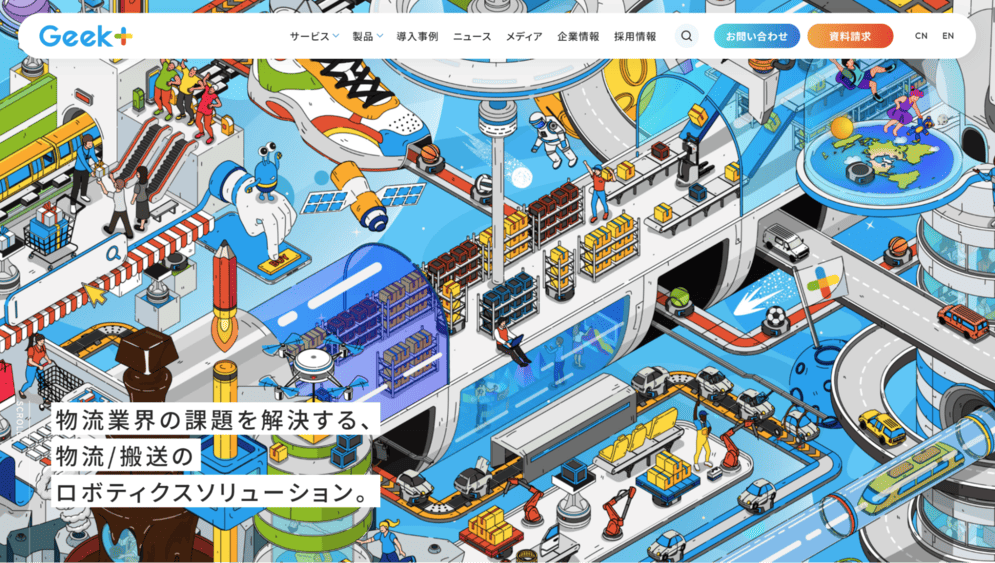
ギークプラスは、物流ロボットの販売・導入から24時間365日のメンテナンス、生産性改善コンサルティングまで一貫したサービスを提供しています。
最先端の自動化ロボットを利用できるフルフィルメントセンターを相模原と2拠点所有しており、ECを中心としたオンライン販売をサポートします。
従量課金制(利用した分のみの課金)を採用しているため、無駄なコストもかからずに運用できます。
また、多様なオーダーへ柔軟に対応し、スペースの最適化によって既存倉庫のスペース問題も解決できます。
【提供している主な自動化ロボットの種類】
ピッキング Pシリーズ |
|
PopPick |
|
ソーティング Sシリーズ |
|
Four-way Shuttle Solution |
|
【基本情報】
会社名 | 株式会社ギークプラス |
所在地 | 東京都渋谷区恵比寿4-20-3恵比寿ガーデンプレイスタワー 26階 |
ホームページ | https://www.geekplus.jp/ |
Roboware
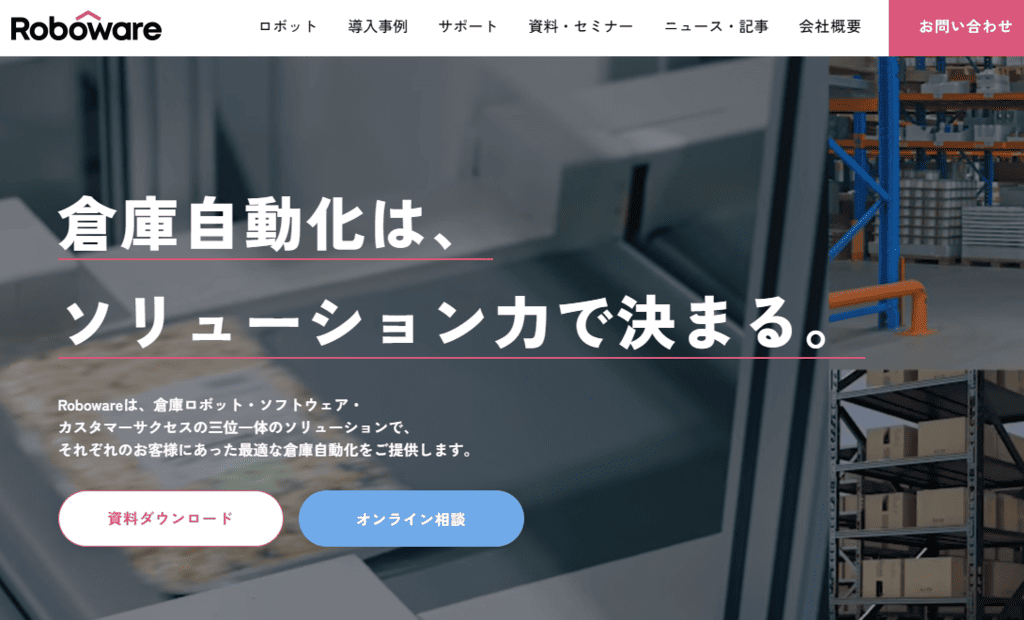
Robowareは、物流現場や倉庫の自動化を支援するロボットソリューションを提供する企業です。
Robowareの倉庫ロボットサービスでは、顧客のニーズや予算に応じて選べる2種類の料金プランを用意しており、初期投資を抑えられる「レンタルプラン」と、保守サービスが可能なサブスクリプション契約の「購入プラン」が選べます。
ロボットの導入から運用、保守に至るまで包括的なサポートを提供し、現場でのトラブル発生時にも遠隔カメラやビデオ通話を活用して、リモートで状況を迅速に把握し、問題解決をサポートします。
【提供している主な自動化ロボットの種類】
Omni Sorter |
|
Flexシリーズ |
|
Ranger GTP |
|
HAIPICK |
|
【基本情報】
会社名 | Gaussy 株式会社 |
所在地 | 東京都港区芝大門2-1-16 +SHIFT SHIBADAIMON 8階 |
ホームページ | https://roboware.ai/ |
+Automation
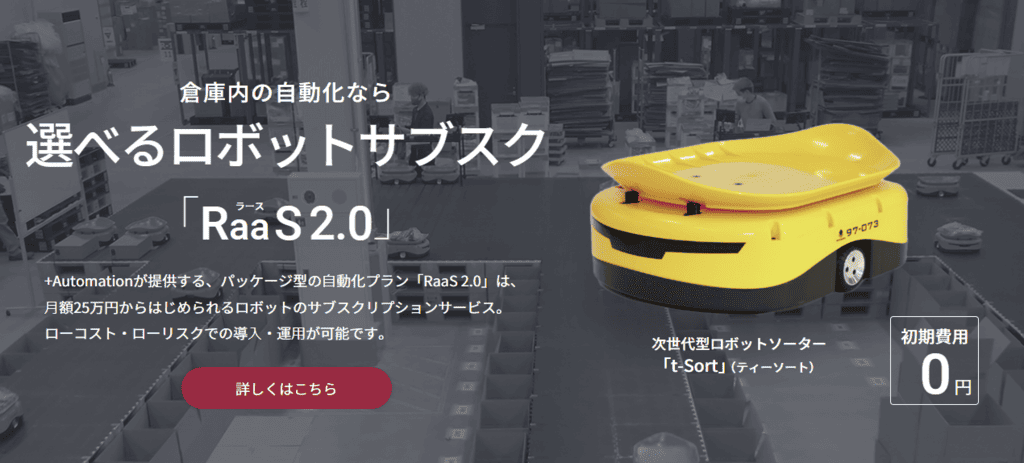
プラスオートメーション(+Automation)は、物流現場の自動化を推進するロボティクス企業です。仕分けロボットのサブスクリプションサービス「RaaS 2.0」を提供しています。
自動化を検討中の企業に向けた、月額25万円から利用できるトライアルプランがあり、トライアル終了後には本格導入に向けたプラン選択が柔軟に行えます。
また、繁忙期にはロボットの台数を増やし、閑散期には減らすといった需要変動にも柔軟に対応可能です。
【提供している主な自動化ロボットの種類】
t-Sortシリーズ |
|
AirRob |
|
【基本情報】
会社名 | プラスオートメーション株式会社 |
所在地 | 東京都江東区大島3-1-6 |
ホームページ | https://plus-automation.com/ |
倉庫内の環境を整える
倉庫内が作業環境が整えられていないと、商品が所定の場所に保管されていなかったり、同じ商品が複数の場所に分散していたりと、在庫の把握が難しくなります。その結果、在庫数に誤差が生じ、欠品や紛失につながる恐れがあります。また、作業動線が乱れていると、ピッキングに時間がかかり、作業効率が大幅に低下します。
そのため、作業しやすいように倉庫内の環境を整えることが重要です。
例えば、以下のような整理方法を取り入れるのがおすすめです。
- 出荷頻度が高いものを入口付近に頻度が低いものを奥に保管する
- 必要なものと不要なものを分類する
- 過剰在庫や不良在庫を処分する
作業環境を変更する際は、あらかじめ社内でルールを決めておき、それに沿って倉庫内の環境を整えましょう。
マニュアルを整備・更新する
出荷業務に関わるスタッフが迷わず作業ができるよう、マニュアルを整備し、作業手順を明確にしましょう。
マニュアルがすでにある場合は、過去に生じたミスと改善点を反映し、最新版に更新することをおすすめします。
改善点を洗い出す方法として、問題が発生した際に「なぜ?」を繰り返し問いかけ、根本原因(真因)を特定して再発防止策を講じる「なぜなぜ分析」という手法が有効です。
例えば、ミスに対して以下のように考えていきます。
例「ある商品が未発送だった」場合の原因の特定
▼なぜ発送されなかったのか?
注文情報が出荷リストに記載されていなかった。
▼なぜ出荷リストに記載されていなかったのか?
注文情報が入力ミスで漏れていた。
▼なぜ入力ミスが発生したのか?
作業員が急ぎで処理していたため確認不足だった。
▼なぜ急ぎで処理していたのか?
繁忙期で作業量が多く、人員が不足していた。
▼なぜ人員不足だったのか?
繁忙期対応の計画が不十分だった。
このように、「なぜ」を繰り返すことで根本原因が特定できます。
原因を特定したら、「人員増加」「作業手順書の整備」「倉庫管理システム導入」などの具体的な改善案を決め、マニュアルにも盛り込み随時更新を行います。
作成したマニュアルは、出荷作業に漏れが出ないようスタッフ全員で共有しましょう。
ダブルチェックを行う
誤出荷や同梱漏れを防ぐには、ダブルチェックの実施がおすすめです。特に、注文内容との照合は、ダブルチェックを取り入れることで、誤出荷の防止につながります。
ダブルチェックの方法は、二人以上でそれぞれ確認する方法と、一人が時間をおいて二度確認する方法があります。
一人で行う場合でも、二回目のチェックで見落としに気付くことがありますが、ダブルチェックを行っても完全にミスを防ぐことは難しいため、倉庫管理システムの活用など他の対策との併用が効果的です。
作業員への教育やトレーニングを行う
作業員への定期的な教育やトレーニングは、作業手順の理解度を深め、ミスの防止や業務の効率化につながります。
教育やトレーニングを通して作業員のスキルが向上すると、出荷作業の精度も安定します。
例えば、動画マニュアルなど視覚的な教材を活用すると、作業員全体の理解度が深まり、作業にバラつきがなくなるでしょう。
受注管理システムを導入する
受注管理システムとは、以下の受注業務全般を一元的に管理するためのシステムです。
- 注文情報の登録
- 管理
- 在庫確認
- 出荷指示
- 請求書発行
受注管理システムを導入すると、数量や商品名の誤入力や、データ転記中の抜け漏れ、処理忘れといった手作業によるミスを防ぎ、業務を効率化が期待できます。
【受注管理システムを導入するメリットとデメリット・注意点】
メリット |
|
デメリット・注意点 |
|
【代表的な機能一覧】
- マルチチャネル管理(EC、電話、SNSなどの受注統合)
- 在庫反映機能(リアルタイム在庫管理)
- 出荷・請求管理
- メール自動返信
- 顧客別マイページや他システムとの連携
ここでは、おすすめの受注管理システムを3つご紹介します。
NEXT ENGINE
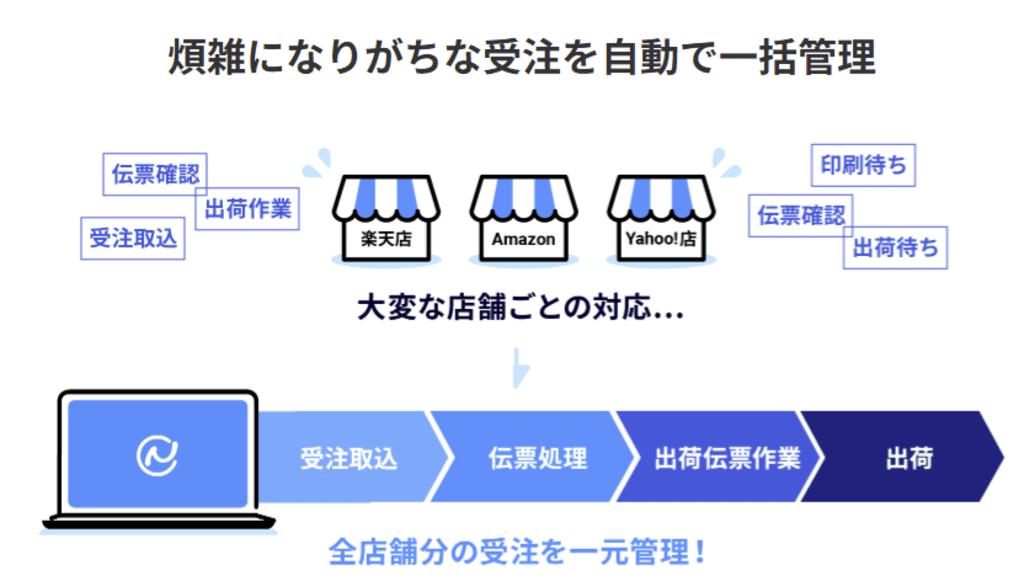
ネクストエンジンは、複数のネットショップやモールの受注・在庫・出荷業務を効率化・自動化するために設計された受注管理システムです。
複数店舗から取り込んだ注文を自動的にステータス振り分け、出荷可能な注文を即座に処理できます。これにより、確認作業の手間を削減し、スピード出荷の実現が可能です。
また、オフラインの注文や倉庫管理システムとの連携も可能です。
同梱可能な注文の自動検出や、送り状の発行、問い合わせ番号連絡までを効率よく行えるなど、出荷業務に役立つさまざまな機能が搭載されています。
【ネクストエンジンがおすすめの事業者】
- 複数のネットショップやECモールを利用している
- オフラインでも注文を受けている
- 一元管理によって効率化を図りたい
【基本情報】
会社名 | NE株式会社 |
所在地 | 神奈川県横浜市港北区新横浜3-2-3 EPIC TOWER SHIN YOKOHAMA 16階 |
ホームページ | https://next-engine.net/functions/jyuchu/ |
GoQSystem
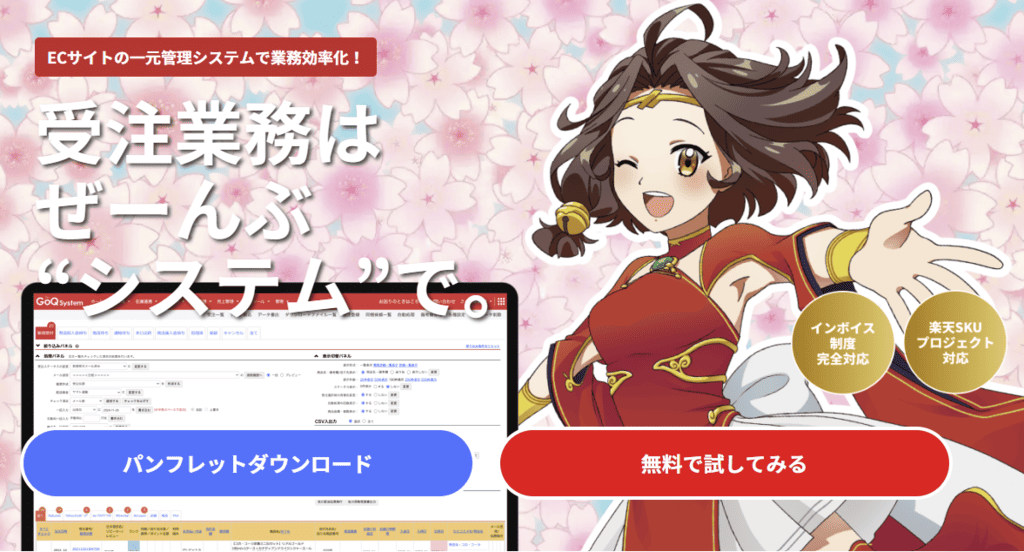
GoQSystemは月額16,500円(税込)から利用できる受注管理システムで、注文数が増えても金額が変わらない定額制が特徴です。
物流倉庫とのAPI連携により、注文から出荷までのプロセスの完全自動化が可能です。
さらに、注文内容に基づいたピッキングリストの自動生成や、配送状況、発送完了通知の自動送信など、機能も充実しています。
最低利用期間は3ヵ月で、受注件数100件/月、受注金額は50万円/月まで利用可能なフリープラン(無料)も用意されており、気軽に導入しやすい点もメリットです。
また、受注管理だけなく、在庫連携や出荷管理まで対応したプランもあり、それぞれ20日間の無料お試しが可能です。
【GoQSystemがおすすめの事業者】
- 複数モールや店舗を運営している
- 出荷件数が多い
- はじめて受注管理システムを導入するため不安がある
【基本情報】
会社名 | 株式会社GoQSystem |
所在地 | 東京都中央区京橋1丁目6-12 NS京橋ビル 5階 |
ホームページ | https://goqsystem.com/ |
コマースロボ
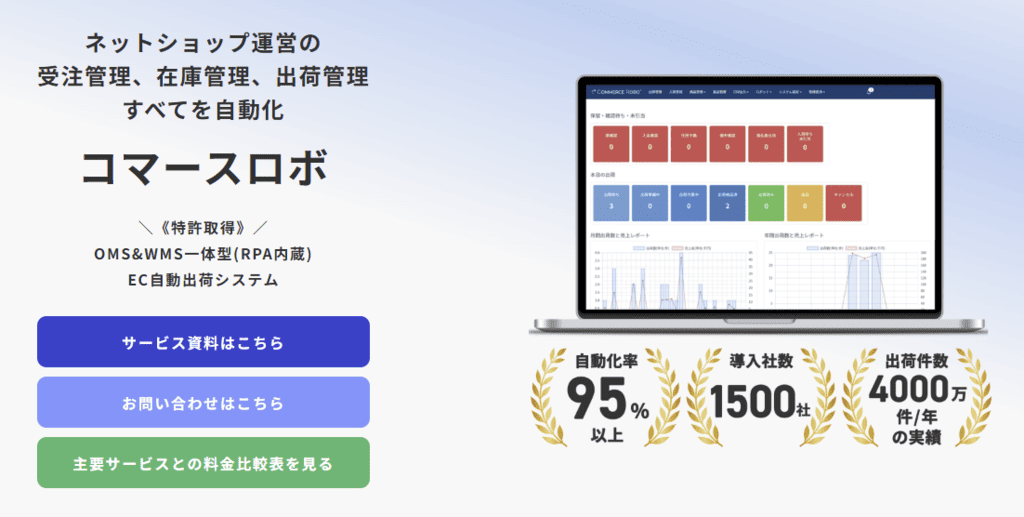
コマースロボは、内蔵された処理ロボット(RPA)により、受注データの精査や確認作業を短縮できる受注管理システムです。
受注管理・在庫管理・出荷管理などのECバックオフィス業務をほぼ自動化し、一元管理が可能です。
受注管理システムと倉庫管理システム(WMS)を一体型で提供しており、高機能なWMSによって在庫管理や入出荷作業を効率化し、ミスの削減が図れます。
初期費用0円で、低額な月額料金な上に出荷件数による従量課金制で無駄なく活用できます。
【コマースロボがおすすめの事業者】
- 出荷業務における人的ミスが多く、改善したい
- 受注管理システムだけでなく倉庫管理システムの導入も検討している
- 初期費用は可能な限り抑えたい
【基本情報】
会社名 | 株式会社コマースロボティクス |
所在地 | 東京都港区新橋5-10-5 PMO新橋Ⅱ 4階 |
ホームページ | https://www.commerce-robo.com/ |
まとめ:出荷業務の効率化には「原因の見極め」と「適切な対策」がカギ
本記事では、出荷業務の概要や正しい手順、誤出荷を防ぐ方法を詳しく解説しました。
EC市場の拡大や消費者ニーズの多様化が進む中で、出荷業務の効率化は物流・EC事業にとって欠かせないテーマです。
出荷業務の効率化を図るには、まず出荷作業の流れを正しく理解し、現状の課題と原因を見極め、適切な対策を積み重ねることが大切です。
具体的には、マニュアルの整備・更新やダブルチェックの仕組みづくり、従業員への教育といった基本的な対策に加え、倉庫内の自動化や受注管理システムの導入など、人手に頼らない仕組みを取り入れるのも効果的です。
出荷業務は、商品が届いた瞬間の顧客体験に直結する重要なプロセスです。
だからこそ、ミスを防ぎ、スムーズな対応ができる体制づくりを目指していきましょう。