物流ロボットとは、物流現場におけるピッキング・仕分け・搬送・保管などの作業を自動化するためのロボットです。近年物流業界ではロボット技術の導入が進み、業務の効率化や省人化が図られています。
しかし、物流ロボットを導入するには、自社の課題に適した機器を選定したり既存システムとの連携性を確認したりとさまざまな検討が必要です。
本記事では、物流ロボットの基本知識からメリット、導入における課題まで詳しく解説します。企業の導入事例も交えながら物流ロボットの活用方法を紹介するので、導入を検討している企業はぜひ参考にしてください。
物流ロボットとは
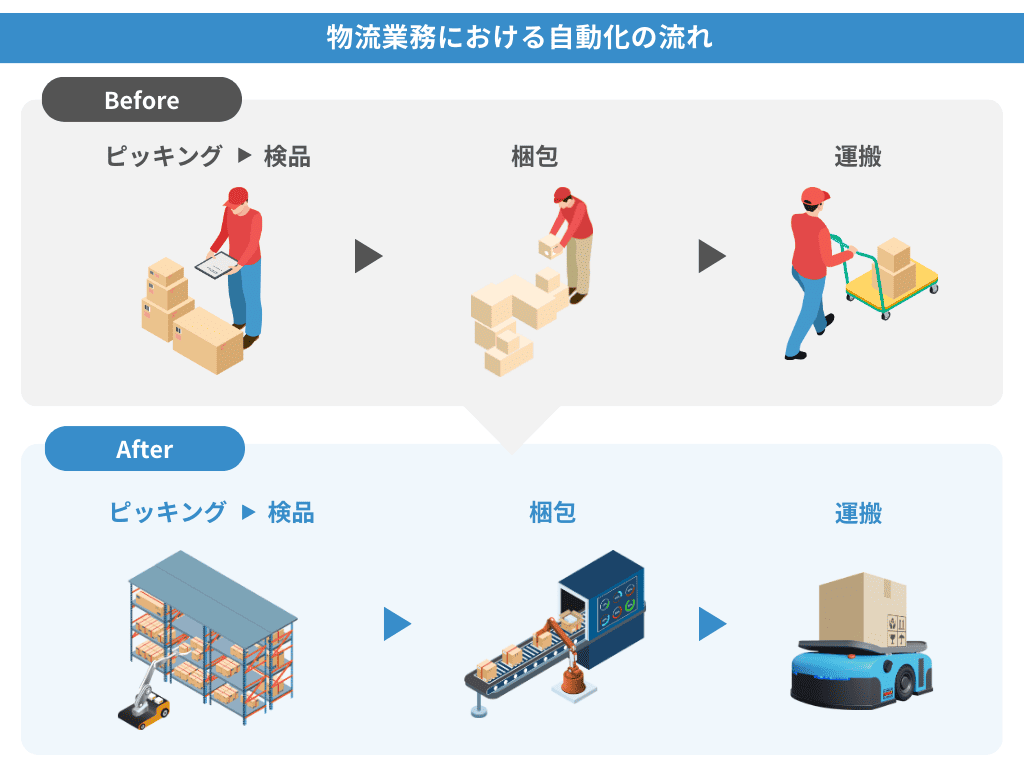
物流ロボットとは、物流現場における荷物のピッキング・仕分け・搬送・パレタイズ・デパレタイズなどの単純業務を自動化できるロボットのことです。
人依存の物流現場では将来物流費用が高騰し、事業収支が悪化する懸念があります。また、繁忙期や年末年始などに人手不足にもなりやすく、安定した運用が難しい課題も抱えています。
そこで、物流オペレーションの中で、自動化できる部分は物流ロボットに任せる必要性が出てきました。
物流ロボットを使えば、人の作業負担を軽減し、倉庫や物流センター内の作業効率を向上させられます。省人化を実現できるのはもちろん、ヒューマンエラーの防止や人材不足の解消を目指せます。
ここからは、物流ロボットの役割や自動倉庫との違いについて深掘りしていきましょう。
物流ロボットの役割
物流ロボットの主な役割は、人と協働しながら現場の省人化・省力化を進めることです。作業の一部を物流ロボットが担うことで人の作業負担を軽減し、作業効率の向上を目指せます。
ただし、物流ロボットは、すべての作業を一任できる万能的な存在ではありません。たとえば、形や質感がバラバラな商品や壊れものなどを繊細に扱うような作業や、細かな外装検品、イレギュラー処理は人でないと対応できません。
そのため、物流ロボットの導入では、人がやるべき作業は人が実施し、「探す」「歩く」といった工数削減効果の高い作業をロボットに任せます。ロボットと人間が協力しながら作業を進めることが、業務効率化の鍵となります。
物流ロボットと自動倉庫の違い
物流ロボットと自動倉庫は、どちらもマテハン機器(マテリアル・ハンドリング:工場や倉庫などで、原材料・仕掛品・商品などを運搬・保管・取り扱う一連の作業やその手法)に分類されます。
物流業務の効率化を目的とした機器ですが、特徴や運用方法に以下のような違いがあります。
項目 | 自動倉庫 | 物流ロボット |
---|---|---|
特徴・概要 |
|
|
メリット |
|
|
デメリット |
|
|
保管の効率化、保管から入出庫までを自動化したいなら自動倉庫が適していますが、固定設備なので汎用性には劣る傾向にあります。
物流ロボットなら搬送やピッキングなど工程ごとに活用でき、すでに稼働している倉庫でも導入しやすいのが魅力です。レイアウトの変更や運用の標準化で幅広い対応ができるため、柔軟性が求められるBtoC物流の現場では特に役立つでしょう。
物流ロボットの市場規模
物流ロボットの市場規模は世界的に拡大しており、Fortune社の市場調査では2029年までに 210億1億USドル(日本円で約28兆3,635億円)に成長すると予測されています。
物流ロボットの需要が増している背景には、新型コロナウイルス感染症によるEコマース分野の成長が関係しています。戦略的に物流ロボットを導入する企業も増加傾向にあり、今後もさらに市場が拡大していくと言えるでしょう。
市場セグメントとしては無人搬送車(AGV)が大きなシェアを占めていますが、自律走行搬送ロボット(AMR)のシェアも拡大しています。AMRはEコマースや倉庫や物流、製造、小売といった業界で導入が進んでおり、リアルタイム配送の顧客需要の増加に伴い、急成長が予測されています。
物流ロボットが期待されている2つの理由
世界的に需要が高まる物流ロボットですが、活用が期待されている理由としては大きく2つが考えられます。
物流ロボットが期待されている2つの理由 |
---|
|
それぞれ詳しく解説するので、物流ロボットが注目されている背景について理解しておきましょう。
物流現場における人材不足の深刻化
日本では少子高齢化が年々加速しており、物流業界でも人手不足が深刻な課題となっています。総務省による「令和4年版情報通信白書」によると、2050年には日本の生産年齢人口が5,275万人に減少すると見込まれており、労働力不足が懸念されています。
また、肉体労働が多い、立地が悪く通勤しにくいなども、物流現場の人材不足が加速している要因のひとつです。物流ロボットは、このような倉庫や配送センターでの人材不足を補う手段として注目されています。
物流の2024年問題によって荷待ち・荷役の時間短縮が必要になったこともあり、倉庫内の業務効率化はますます重要性が高まるでしょう。
物流ニーズの高度化
EC市場の拡大によって、消費者の物流ニーズはますます高度化しています。多品種・小ロットの配送も増加傾向にあり、従来の大量一括出荷型の物流システムでは対応が困難になってきました。
個人向けの小口配送では、大量のSKUから商品をピッキングし、注文ごとに梱包するため、工数が多くなります。加えて、当日・翌日発送が求められるようになり、物流現場では物流のスピード向上が急務です。顧客ニーズは日々変化しており、柔軟に対応できる物流体制の構築が求められます。
物流ロボットの種類一覧
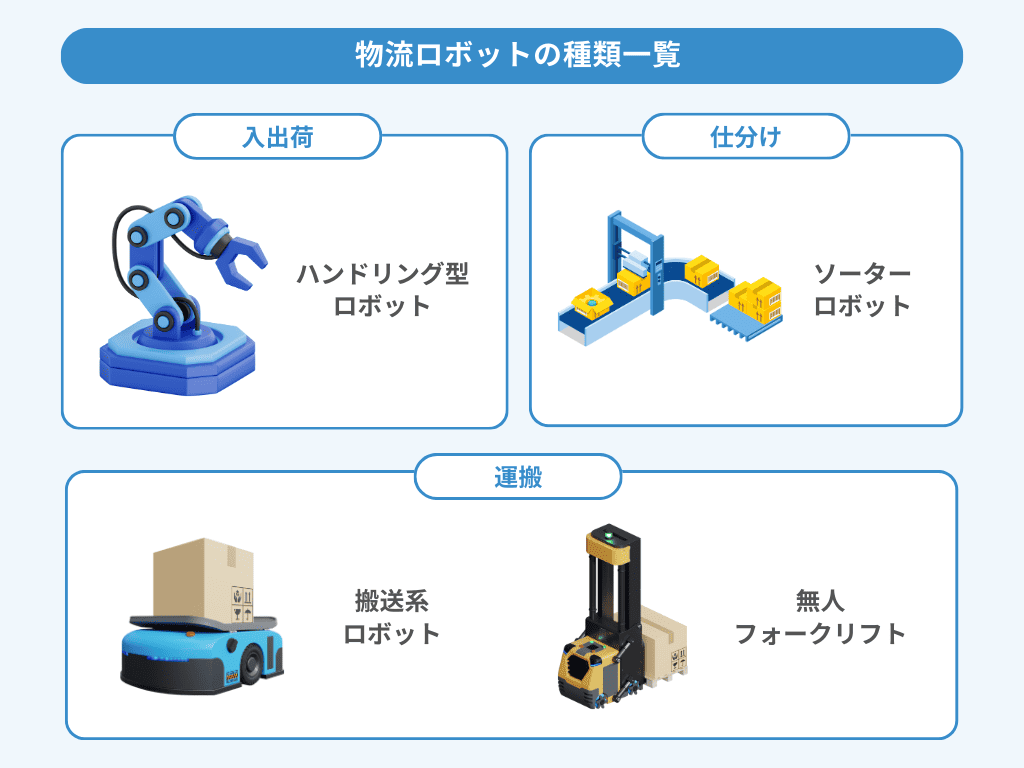
物流ロボットと一口に言っても、用途によってさまざまな種類があります。
物流ロボット | 概要 | 導入が向いているケース |
---|---|---|
搬送系ロボット | 倉庫や物流センター内で荷物を運ぶ役割を担うロボット | ・大量の商品を頻繁に移動する場合 ・「歩く」「探す」工程に課題がある場合 |
ソーターロボット | 商品を配送先や地域別に自動で仕分けるロボット | ・大量の商品の仕分けが必要な場合 ・さまざまな種類の商品を扱っている場合 ・仕分け作業の人材不足が課題になっている場合 |
ハンドリング型ロボット | 商品を持ち上げたり移動させたりする作業を自動化するロボット | ・重量のある商品や大型商品を扱っている場合 ・荷役作業に関する作業負荷に課題がある場合 |
無人フォークリフト(AGF) | 荷物の搬送を無人で行えるフォークリフトロボット | ・従業員の安全性を確保したい場合 ・フォークリフトが操作できる人材が不足している場合 ・重量のある商品や大型商品を扱っている場合 |
それぞれ搬送やピッキングなど特定の作業に特化しているので、解決したい課題に合わせて適切なロボットを選択することが大切です。
ここからは物流業務の効率化に寄与する、代表的な物流ロボットを紹介します。
1.搬送系ロボット
搬送系ロボットは、倉庫や物流センター内で荷物を運ぶ役割を担うロボットです。
保管棚を搬送して作業者のもとに商品を運ぶGTP方式のソリューションや、ピッキング棚まで人を誘導して商品を運ぶピッキングアシスト型ソリューションなど、搬送系ロボットの使い方はさまざまです。
搬送系ロボットは、走行方式によって自律走行ロボット(以下AMR)と無人搬送ロボット(以下AGV)の2種類に分かれます。ここからは、AMRとAGVの特徴や違いについて詳しく見ていきましょう。
運送系ロボットの種類 |
---|
|
1-1.自律走行ロボット(AMR)
AMR(Autonomous Mobile Robot)は、自己判断で最適なルートを選びながら移動できる自律走行型の搬送ロボットです。レーザーや画像認識によって障害物を検知し、目的の場所まで移動します。
決まったルートを進むわけではないので、人の動きに応じて臨機応変な対応をしやすい点が特徴です。人と協働しやすく、同じエリア内で作業がしやすくなっています。
GTP(Goods-To-Person)とは |
---|
GTPとは、物流センターや倉庫において商品を棚ごと作業者の元へ運ぶ方式(ピッキング支援システム)です。GTPは運用システムやシステムの概念そのものを指し、GTPを実現するロボットとして、AGVやAMRが使用されています。 |
1-2.AGV(無人搬送ロボット)
AGV(Automated Guided Vehicle)は、あらかじめ設定されたルートを自動で走行するロボットです。工場や倉庫内の決められた経路を移動し、一定の場所から別の場所へ荷物を搬送します。
AGVは、工場の生産ラインや物流センターなど決まった動線のある環境におすすめです。一般的にはQRコードや磁気テープを引いて動かしますが、AMRのように自律走行が可能なAGVも登場しています。
AMRとAGVの違い | 導入効果が高いのは?
AMRとAGVはどちらも「搬送」の役割を担う物流ロボットですが、走行方式に大きな違いがあります。
搬送系ロボットの種類 | AMR | AGV |
---|---|---|
走行方式(特徴) |
|
|
メリット |
|
|
デメリット |
|
|
適用環境 | レイアウトの変更が多いEC倉庫や物流センター | ルートが固定された工場や倉庫 |
AMRは目的地まで自律走行しますが、AGVが走行できるのは決められたライン上だけです。ただしAGVの中にも自立走行可能なモデルがあり、一概にAMRのほうが導入効果が高いとは言えません。
実際にギークプラスでは、固定アンカー(ガイド)なしで稼動するAGVを扱い、柔軟性を備えています。自社に搬送系ロボットを導入する際は、物流環境や業務の特性に応じて最適なロボットを選定しましょう。
▼参考記事
物流ロボット(AGV・AMR)の活用・導入効果を正しく理解するためのポイント~国内市場で散見される誤解
2.ソーターロボット
ソーターロボットは、商品を配送先や地域別に自動で仕分けるロボットです。商品の仕分け作業は物流業務の中でも時間を要する工程ですが、ソーターロボットを使えば高速かつ正確に商品を仕分けできます。
ソーターロボットは、商品に付与されたバーコードやRFIDタグを読み取り、事前に設定された配送先や種類ごとに自動で仕分ける仕組みです。大量の商品を短時間で分類するので、商品の仕分けにかかる時間を短縮できます。
なお、ソーターロボットには、ベルトコンベヤ型・平面型・立体型などさまざまな形があります。ギークプラスでは、平面仕分けや複数階を跨いだ仕分けを効率化するロボットを多数提供しています。詳しく知りたい方は、ぜひ下記のページをご覧ください。
3.ハンドリング型ロボット
ハンドリング型ロボットは、商品を持ち上げたり移動させたりする作業を自動化するロボットです。ロボットアームやロボットハンドを搭載しており、ピッキングや積み下ろし作業を任せられます。
ハンドリング型ロボットには、作業内容に応じて以下のような種類が存在します。
ハンドリング型ロボットの種類 |
---|
|
各ロボットについて詳しく解説するので、用途に合ったロボットを探してみましょう。
3-1.ピースピッキングロボット
ピースピッキングロボットは、物流倉庫などで個々の商品をピッキングするロボットです。ロボットアームで該当する商品を持ち上げ、出荷最小単位でピッキングします。
商品の形状や大きさに応じて最適な配置でピッキングできるので、ヒューマンエラーが発生しやすい大量のオーダー処理に向いています。
3-2.ケースピッキングロボット(パレタイズ・デパレタイズロボット)
ケースピッキングロボットは、段ボールやケース単位でピッキングできるロボットです。パレタイズ(積み上げ)やデパレタイズ(積み下ろし)の作業を自動化する役割を担います。
パレタイズロボットは運送や保管のために商品をパレットの上に積み上げ、荷崩れしないように固定する作業を自動化可能です。一方、デパレタイズロボットは、パレットから商品を降ろす作業を自動化できます。
ケースピッキングロボットを導入すれば、大型の商品や重量のあるケースを取り扱う際に、事故のリスクを軽減できる点が魅力です。作業効率化だけでなく、物流現場の安全性向上に努めたい企業は導入を検討してみましょう。
3-3.バンニング・デバンニングロボット
バンニング・デバンニングロボットは、コンテナやトラックへの貨物の積み込み(バンニング)や荷下ろし(デバンニング)を自動化するロボットです。
トラック荷台やコンテナ内の荷役作業は人による作業が中心でしたが、ロボットの導入によって作業の省人化が期待できます。大前提として、バンニング・デバンニング作業は過酷です。商品の重さや夏の暑さによる肉体労働を解消し、労働環境の改善に役立ちます。
4.無人フォークリフト(AGF)
無人フォークリフト(以下AGF)は、荷物の搬送を無人で行えるフォークリフトロボットです。AGFはレーザーレーダーやカメラ、センサーを搭載しており、障害物を避けながら荷物を搬送できるのが特徴です。一般的に搬送対象はパレット積みの商品で、入出荷エリア間の繰り返し作業に適しています。
固定されたガイドラインに従う従来型AGVと比較して、比較的自由にレイアウトを組みやすく、限られたスペースでも生産性が向上できるよう稼働できます。
人の操作が不要なのでフォークリフト操作時の事故やヒューマンエラーによる荷物の落下などを防止できる点もポイントでしょう。
フォークマンの人件費はすでに高騰が始まっているため、今後の物流コスト抑制対策としても、効果が期待できます。ただし、導入費用も高額なため、費用対効果を見極める必要があります。
物流ロボットを導入する4つのメリット
本章では、物流ロボットを導入する4つのメリットを紹介します。
物流ロボットを導入する4つのメリット |
---|
|
物流ロボットの活用に迷っている企業はぜひ参考にしてください。
省人化と業務効率の向上
物流ロボットを導入すれば、人に依存していた作業を自動化でき省人化につながります。物流ロボットによっては、処理スピードが人間の数倍と言われており、ロボットが代替することで業務効率化が期待できるでしょう。
また、物流ロボットは、人間と異なり24時間365日稼働させることが可能です。業務の稼働率を最大化できるため、急な需要の増加にも柔軟に対応できます。
ヒューマンエラーの防止
物流現場では、下記のようなヒューマンエラーが課題になるケースがあります。
【物流現場でのヒューマンエラーの例】 |
---|
|
物流ロボットを導入すると、ヒューマンエラーをカバーしながら作業ができるようになります。たとえば、ソーターロボットを導入すれば、仕分け時のミスを予防できるため、誤出荷を減らせます。
ただし、物流ロボットの導入をするために、業務の標準化を進める必要はあるでしょう。
リードタイムの短縮
物流ロボットを導入すれば無駄な移動時間を削減でき、作業のスピードが向上します。リードタイムの短縮につながり、短時間で確実に荷物を届けられるのがメリットです。
近年ではEC市場の成長によって、即日配送や翌日配送といったスピード対応が求められています。物流ロボットは商品の迅速な配送や発送をサポートするので、顧客満足度の向上やリピーターの増加も期待できるでしょう。
労働環境の改善
物流現場では重労働や長時間労働が問題視されており、労働環境の改善が求められています。特に重量物の搬送やフォークリフトの操作には危険が伴い、労働災害の原因にもなり得るでしょう。
物流ロボットを導入すれば、このような危険な作業や労力の大きい作業をロボットに任せられるのが魅力です。人間の作業負担を軽減できるのはもちろん、安全性の向上にもつながります。
物流ロボットを導入するときの課題
物流ロボットには業務効率の向上やヒューマンエラーの防止といったメリットがありますが、導入時にはいくつかの課題も伴います。
物流ロボットを導入するときの課題 |
---|
|
物流ロボットによる効果を最大化するには、これらの課題に対して適切な対策を講じることが大切です。物流ロボットの導入で直面しやすい課題を詳しく解説します。
導入時にコストがかかる
物流ロボットの導入では、ロボット本体の価格に加えてインフラ整備やシステムとの連携費用など、多くの初期投資が発生します。長期的な費用対効果は高くなる可能性がありますが、導入時に高額なコストがかかる点に注意が必要です。
初期費用は物流ロボットの費用は設備や規模によって異なりますが、高機能なロボットだと数千万〜数億円の費用がかかる可能性もあるでしょう。定期的なメンテナンス費用も必要なので、総合的なコストを事前に計算しておくことが大切です。
社員のリテラシーが必要になる
物流ロボットを導入すると業務フローが大きく変化するため、社員へのリテラシー教育が必要です。基本的な操作方法やメンテナンス方法を熟知していなければ、予期せぬトラブルにつながる恐れがあります。
また、物流ロボットの導入では、ロボットの監視やメンテナンスなど新たな業務が発生することも考えられます。企業側は導入前に社員教育や専門人材採用の計画を立て、スムーズに運用できるよう準備を進めることが重要です。
緊急時のバックアップ体制が必要になる
物流ロボットは基本的に高い精度で稼働しますが、システムエラーが発生する可能性もゼロではありません。停電やシステム障害によってロボットが稼働しなくなると物流が止まり、大きな損失につながるリスクがあります。
緊急時の損失を最小限に抑えるには、緊急時のバックアップ体制を整備しておくことが大切です。ロボットの故障に対応できるメンテナンスチームを整備し、トラブルに備えておきましょう。定期的な点検で、物流ロボットの稼働状態を確認するのも有効です。
事業変化に対応できる設備が求められる
物流業界では、市場の変化や消費者ニーズの多様化によって倉庫運用や取り扱い商品、物量が急速に変化することも珍しくありません。事業の変化に対応できるロボットを選ばなければ、早期にレイアウトの再構築や再投資が必要になる可能性があります。
事業変化に対応できる設備を選ぶなら、床へのアンカー固定などの工事が不要な可動式の物流ロボットがおすすめです。柔軟性が高いので、倉庫内のレイアウト変更や出荷量の変化にもスムーズに対応できます。
費用対効果の算出が難しい
物流ロボットの導入には高額な費用がかかりますが、長期的な費用対効果を見極めるのは容易ではありません。特に導入後の業務効率向上や人件費の削減効果を数値化するには、詳細なデータ分析が求められます。
費用対効果の算出はもちろん、そもそも物流ロボットの導入が自社に適しているか検討するのも難しい課題です。業務フローや取り扱う商品の種類、抱えている課題、倉庫の規模などによって最適な設備が変わるため、物流ロボットの選定にも時間がかかるでしょう。
費用対効果を算出するには、導入前に試験運用を行い、実際の効果を検証することが重要です。
物流ロボットを導入するときの5つのポイント
物流ロボットの導入を成功させたいなら、以下5つのポイントを押さえておきましょう。
物流ロボットを導入するときの5つのポイント |
---|
|
物流ロボットを導入するときは、ロボットが果たす役割を明確にし、現場の環境やシステムとの整合性を確保する必要があります。ここからは各ポイントについて詳しく解説します。
自社課題に応じて物流ロボットの業務範囲を決める
物流ロボットを導入するだけで、すべての業務を自動化できるわけではありません。まずは自社の課題を明確にし、ロボットが担う業務範囲を設定しましょう。
ロボットの活用範囲を狭めすぎると十分な効果を得られない可能性がありますが、広げすぎても運用が複雑になり、現場への負担が大きくなるリスクがあります。
そのため導入前には、倉庫内の作業工程や動線、作業ごとの所要時間や頻度などを可視化・整理し、どの業務をロボットに任せるべきかを慎重に検討することが大切です。
自社システムとの連携性を確認する
物流ロボットを導入する際は、既存システムとの連携性もチェックしておきましょう。自社の倉庫管理システム(WMS)やロボット間で連携できないと、追加のカスタマイズが必要になる場合があります。その場合、費用の追加が避けられません。
そのため導入前には、ロボットの連動性や柔軟性をメーカーに確認しておくのがポイントです。事前にシミュレーションを行い、ロボットが連携して機能するか検証しておくと安心でしょう。
物流現場のレイアウト変更を検討する
物流ロボットを導入するときは、必要に応じて物流現場のレイアウト変更を検討しましょう。効率的に運用するためにもロボットの動線を確保し、作業スペースを最適化することが大切です。
物流業務が一時的に滞るリスクがあるので、倉庫の増設や移動といったタイミングで物流ロボットを導入するのがおすすめです。
レイアウトを変えられない場合は、AMRなど既存の通路を活用して人の移動を補助できるタイプのロボットが選択肢となります。物流現場のレイアウトによっては他のロボットも導入できる可能性があるので、メーカーと協議しながら進めると良いでしょう。
オペレーションの見直しをする
物流ロボットの導入後に、従来のオペレーションをそのまま適用することはできません。作業の流れや人間の役割が変わるため、ロボットの特性に合わせてオペレーション全体を見直す必要があります。
オペレーションの見直しでは、業務プロセスの標準化を図るのがポイントです。ロボットは事前に決められたルールにしたがって動作するので、だれが使っても同じ効果を得られるように標準化を進めることが求められます。
カスタマイズが必要な部分と標準化できる部分を切り分け、効率的な運用を推進しましょう。
ロケーションの最適化と稼働後のメンテナンスを念頭に置く
物流ロボットの中でも長期的にAGVやAMRを活用するには、ロケーションの最適化とメンテナンス体制の整備が必要不可欠です。
ロボットが頻繁に行き交うエリアに障害物が多かったり、作業スペースが狭すぎたりするとロボットの動作が制限され、期待した業務効率化を実現できない可能性があります。ロボットの動線がスムーズになるよう、適切な配置に調整しましょう。
在庫自体のロケーション最適化も、不可欠です。たとえば、作業者の手待ちが発生しないよう、その時々の売れ筋商品を把握し、保管棚を分散させて滞留を防ぎます。
また、稼働後のメンテナンスについても、導入前から計画を立てておくことが重要です。メンテナンスを怠るとロボットの故障リスクが高まり、業務がストップする原因になります。
最適なロボットの配置やメンテナンスに不安がある企業は、ギークプラスのフルフィルメントサービスの利用も検討してみてください。
物流ロボットの導入事例
最後に、物流ロボットの導入事例を紹介します。導入前の課題や導入したロボットの種類も交えて解説するので、導入イメージをつかむ参考にしてください。
ビックカメラ・ドットコム
ビックカメラ・ドットコムでは、約130万点もの商品を扱うECサイトの物流効率化を目指し、ギークプラスの物流AIロボットを導入しました。
具体的には、約4,900平方メートルの倉庫(EVEエリア)に、約90台のピッキングロボットと約1,500台の棚を設置。15台のワーキングステーションも配置し、効率的な物流オペレーションを実現しています。
▼こちらの事例は下記でも詳しく解説しています。
株式会社アルペン
株式会社アルペンでは、急速に拡大するEC市場に対応するためにEC物流拠点を移転し、物流AIロボットの導入を開始しました。
アッカ・インターナショナルと連携し、段階的にロボットソリューションを拡張。
当初は56台のピッキングロボットと約1,000台の棚を導入し、2020年には40台のロボットを追加しました。
また2021年には同拠点をロボット専用センターに転換し、120台のピッキングロボットと約1,200台の棚を新たに導入しました。現在では7,000坪の自動搬送ロボット専用センターで、合計216台のピッキングロボットと約3,207台の棚が稼働しており、19台のワーキングステーションも設置されています。
大規模なロボット導入によって、ピッキング効率は手作業と比較して約3倍、保管能力は2倍、出庫能力は3倍に向上。EC需要の拡大に柔軟に対応し、顧客への納品リードタイムの短縮や人員不足の課題解決を実現しています。
▼こちらの事例は下記でも詳しく解説しています。
【アルペン】ロボットの段階的拡張により、年々拡大するEC需要に対応
物流ロボットで人材不足の解消と業務効率の向上を実現しよう
物流ロボットは、物流現場における人材不足の解消や業務効率の向上に大きく貢献します。
しかし、ロボットはあくまでも「ツール」に過ぎないため、単に導入するだけでは十分な効果を得られません。ロボットの特性や運用ノウハウを理解し、現場に適した形で活用することが重要です。
本質的な物流課題の改善や物流業務全体の最適化を図るなら、フルフィルメントサービスの活用も検討してみましょう。
ギークプラスでは、自動化設備を活用した物流業務委託サービスを提供しています。従量課金制で段階的に利用できるので、高額な初期投資に不安がある企業におすすめです。詳しく知りたい企業は、ぜひお気軽にお問い合わせください。