デジタルピッキングシステムとは、物流や製造現場でのピッキング作業を支援するシステムです。
デジタルピッキングシステムを導入すれば、作業者はデジタル表示器の指示に従ってピッキングができるため、人的ミスを大幅に削減できます。
デジタルピッキングシステムにはいくつか種類があり、事業規模や商品の特性に合わせて選定することが重要です。
本記事では、デジタルピッキングシステムの基礎知識やシステムの選定方法、おすすめのシステムを紹介します。
デジタルピッキングシステムの導入を検討している方は、ぜひ最後までお読みください。
デジタルピッキングシステムとは
デジタルピッキングシステム(Digital Picking System)は、棚に設置された表示機器で作業指示を伝える電子機器です。
このシステムを導入することで、誰でも簡単にかつ無駄のない動きでピッキングが行えるため、作業効率が上がりミスも大幅に削減できます。
食品やアパレル、医薬品、量販店、製造業など幅広い業界の現場で活用されています。
デジタルピッキングシステムの仕組み
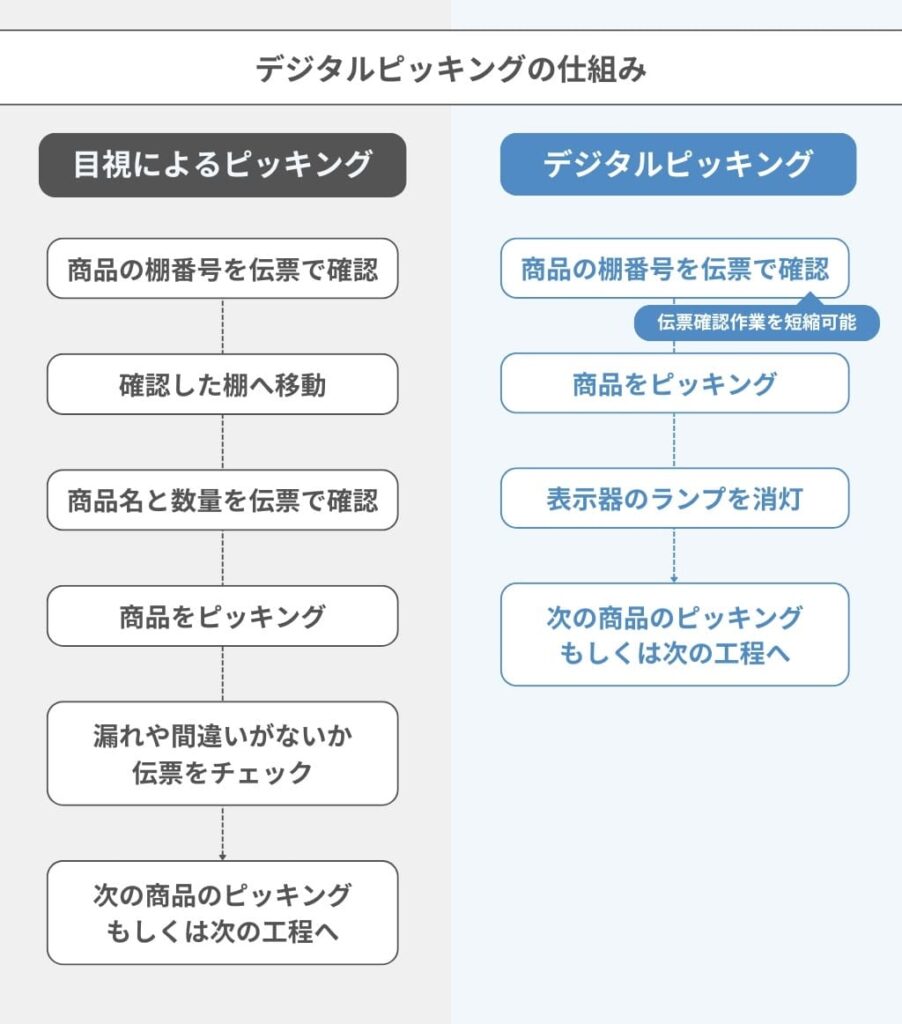
デジタルピッキングシステムは、商品が保管されている棚やコンテナに無線式または有線式のデジタル表示器が設置され、表示機の指示に従って作業者がピッキングを行う仕組みです。
入庫時に商品の置き場所を決定し、品名や数量などの商品情報をシステムに登録します。受注情報に応じて出庫や仕分け内容が表示器に反映され、ランプが点灯することで作業者にピッキング指示が伝えられます。
作業者は表示された指示に従い、棚から商品を取り出し、完了ボタンを押して次の棚へ移動する手順です。
デジタルピッキングシステムの中には、スマートフォンを利用したモバイルピッキングシステムや、バーコードを読み取るハンディターミナルと併用できるものもあります。
ピッキング作業の重要な役割
ピッキング作業は出荷前の重要な工程であり、多くの商品を正確かつ効率的な処理が求められます。
ピッキング作業が遅延した場合、配送スケジュールへ影響を及ぼすだけでなく、製造業の生産ラインにも悪影響が及ぶ可能性があります。
また、ピッキングミスは誤配送を招き、顧客満足度の低下にもつながります。
さらに、重量物を扱うケースもあるため、作業員の体力面にも配慮が必要です。
ピッキング作業における5つの課題
ピッキング作業における課題には、以下の5つが挙げられます。
- ピッキングミスが発生しやすい
- 商品を見つけるまでに時間を要する
- 商品棚までの移動が非効率になる
- 作業員に負担がかかる
- 在庫管理が煩雑になる
これらの課題を詳しく解説します。
ピッキングミスが発生しやすい
ピッキング作業の課題の一つに、ミスが発生しやすいことが挙げられます。具体的には、次のようなミスがよく見られます。
- 商品の取り違え
- 数量間違い
- 期限切れ商品のピッキング
- 類似商品の混同
- 付属品の入れ忘れ
特に、手作業で管理している現場では、このようなミスが起こりやすい傾向です。
ピッキングミスが発生すると、誤出荷や納品トラブルにつながり、顧客からのクレームや返品といった対応が発生する恐れがあります。
商品を見つけるまでに時間を要する
ピッキング作業でよくある課題の一つが、商品を見つけるまでに時間がかかることです。これは、ロケーションミスやピッキングリストの見づらさが原因です。
このような状況では、作業者が商品を探すのに手間取り、作業効率が低下します。その結果、出荷の遅延や納期のズレが生じ、業務全体のスケジュールに影響を及ぼす恐れがあります。
誰が作業してもスムーズに商品を取り出せるようにするには、保管場所の適切なロケーション管理や、ピッキング情報の表示方法の見直しといった対策が必要です。
商品棚までの移動が非効率になる
商品棚までの導線設計が不十分な場合や通路が狭い倉庫では、作業員の移動が非効率になるという課題があります。
例えば、出荷頻度の高い商品が奥に設置されていると、作業員が頻繁に倉庫の奥まで移動する必要があり、その分移動にかかる時間が増えるでしょう。このような状況が繰り返されると、ピッキング作業全体の効率が低下し、作業者の負担も増します。
そのため、作業導線や出荷頻度を考慮した適切なレイアウト設計が求められます。
作業員に負担がかかる
作業者に負担がかかることも、ピッキング作業における課題です。
例えば、以下のような負担が生じます。
- 商品の大きさや重さ、棚の構造が影響し取り出しにくい
- 商品棚の配置が不適切で移動距離が長くなる
- 類似商品が近くに配置されており、判別に慎重な確認が求められる
- 紙のピッキングリストが視認性に欠け読み取りにくい
作業員への負担を軽減するには、入荷時に商品のハウスコード(事業者が決めた商品管理用のバーコード)を貼付し、棚の配置や収納方法を見直す必要があります。
ただし、すべての商品にハウスコードを添付し在庫管理を徹底すると、入荷作業のスピードや効率が低下する可能性があります。
そのため、ピッキング作業の効率化と在庫管理のバランスを取ることが重要です。
在庫管理が煩雑になる
ピッキング作業を手作業に依存している場合は、在庫数の更新や管理がリアルタイムで行われず、在庫管理が煩雑になります。
在庫管理が煩雑になると在庫の過不足が生じやすくなり、過剰在庫や欠品のリスクが高まります。過剰在庫が続けば、保管コストや在庫管理の手間が増加し、最終的には企業全体の利益にも悪影響を及ぼす可能性があるでしょう。
デジタルピッキングシステムのメリット
デジタルピッキングシステムを導入することで、前述の諸課題を解決しながら、以下のことを実現できます。
- ヒューマンエラーを防止できる
- 作業効率が向上する
- 在庫データをリアルタイムで管理できる
- 諸経費を削減できる
ここでは、デジタルピッキングシステムのメリットを詳しく解説します。
ヒューマンエラーを防止できる
デジタルピッキングシステムを導入することで、デジタル表示器による正確な指示により、商品の取り間違いや数量ミスといったヒューマンエラーを防止できます。これにより、誤出荷や在庫管理における課題を回避することが可能です。
例えば、紙のピッキングリストを使用している倉庫では、ピッキング情報の読み間違いや商品の取り間違いなどが発生する可能性があります。
しかし、デジタルピッキングシステムとハンディターミナルを活用すれば、より精度の高いピッキングが実現できます。
作業効率が向上する
デジタルピッキングシステムを導入すると、ピッキング作業の時間が大幅に短縮され、作業効率が向上します。
商品の保管場所や数量がデジタル表示器で指示されるため、紙の伝票を照らし合わせるような作業を行う必要がありません。
ピッキング時に作業者が感じる探す手間や、確認作業の負担などのストレスも軽減できるため、生産性の向上にもつながります。
例えば、自動車部品を取り扱う製作所では、数千点に及ぶ部品を管理する必要があり、ピッキング作業の煩雑化が課題となっていました。
そこで、デジタルピッキングシステムを導入し、部品ごとの情報をリアルタイムで追跡できるようになり、さらに、デジタル表示器により作業フローが簡素化され、作業員が必要な情報を迅速に把握できるようになりました。その結果、ピッキング作業効率が30%アップしたという事例があります。
在庫データをリアルタイムで管理できる
デジタルピッキングシステムを活用すると、在庫データをリアルタイムで管理できるため、在庫の「見える化」ができます。
リアルタイムで正確な在庫数が分かると、過剰在庫の発生や欠品を防止につながります。
また、どの商品がいつ・どれくらい売れたのかが把握できるため、特に繁忙期の変動が大きいEC事業者もスムーズに対応しやすくなります。
デジタルピッキングシステムによる在庫データは、現在の在庫数と過去の出庫履歴が正確に確認できるため、需要予測にも役立つでしょう。
諸経費を削減できる
デジタルピッキングシステムは、以下のような諸経費の削減も期待できます。
- 人件費
- 人材育成コスト
- 印刷費・紙代
人件費(固定費)
デジタルピッキングシステムにより必要な人員数が削減され、人件費を抑えることが可能です。
例えば、食材を配送する物流センターでは、最大10人で行っていたピッキング作業が、デジタルピッキングシステムの導入により、最大6人で対応できるようになった事例もあります。
ピッキングに必要な人員を削減することで、余剰人員を他の業務に充てられるため、物流業務全体の効率化が期待できるでしょう。
人材育成コスト(投資)
デジタルピッキングシステムを導入すると、従業員がスムーズにピッキングを行えるため、人材育成の負担が軽減できます。
例えば、以下のような育成にかけるコストや時間の削減が可能です。
- ピッキング作業におけるハンディターミナルの操作教育
- ロケーション管理のルール教育
- 作業ミスを減らすための改善研修
デジタルピッキングシステムの導入により従業員の作業手順が標準化されるため、作業の品質が安定し、個人差による作業のバラつきも解消できるでしょう。
印刷費・紙代
スマートフォンやタブレットと連携できるデジタルピッキングシステムを導入すれば、紙のピッキングリストが不要になります。
ペーパーレス化により印刷費や紙代を削減が可能になり、環境への配慮にもつながるでしょう。
デジタルピッキングシステムのデメリット
デジタルピッキングシステムを導入する場合、以下のようなデメリットも存在します。
- システム導入や維持にコストがかかる
- 商品の保管場所が固定される
- システムトラブルが発生する可能性がある
これらのデメリットを詳しく解説します。
システム導入や維持にコストがかかる
デジタルピッキングシステムは、物流倉庫内にシステム用のPCやLAN配線を設置する必要があり、構築する際には初期費用が必要です。また、導入後も保守管理や毎月の使用料などのランニングコストが発生するため、継続的に費用が発生することがデメリットです。
しかし、システム導入時には初期投資がかかりますが、既存設備の活用やシステムのカスタマイズにより、初期投資を抑えられるケースもあります。そのため、導入を検討する際は、導入によって削減できるコストを具体的に算出し、費用対効果を見極めることが重要です。
商品の保管場所が固定される
デジタルピッキングシステムのデメリットとして、商品の保管場所が固定される点が挙げられます。保管場所を変更したい場合は、システム設定の修正が必要です。
ただし、保管場所が頻繁に変わる倉庫では、フリーロケーション(保管場所を固定せず流動的に管理する方法)に対応した製品を活用することも可能です。例えば、無線のデジタルピッキング表示器を利用すれば、台車やカゴ車、ピッキングカートなどに簡単に設置できるため、フリーロケーション型の倉庫でも十分に対応できるでしょう。
そのため、頻繁に保管場所を変更する必要がある倉庫では、フリーロケーションに対応している製品かを事前に確認しておきましょう。
システムトラブルが発生する可能性がある
停電やシステム障害などのシステムトラブルが発生すると、デジタルピッキングシステムが停止する可能性があります。
この場合、手動でのピッキングに慣れていない従業員は、トラブル時の対応に時間がかかり、業務効率の低下にもつながります。
このようなリスクを回避するためには、システムの自動化を進めると同時に、災害、事故、システム障害などの緊急事態に備えた「事業を止めないための計画(BCP)」を立案することが重要です。
具体的な対策としては、以下のような方法があります。
- 複数の物流拠点を設定する
- データバックアップの確保
- オフライン運用体制の構築
- システム監視体制の強化
これらの対策を講じることで、急なトラブルが発生した際にも迅速に対応できるでしょう。
デジタルピッキングシステムの導入形態の種類と特徴
デジタルピッキングシステムには、3種類の導入形態があります。
- スタンドアローン型
- オンプレミス型
- クラウド型
3つの特徴と、どのような倉庫に適しているのかを解説します。
スタンドアローン型
スタンドアローン型は、他のデバイスやネットワークに依存せず、単独で機能するシステムです。ネットワーク接続が不要なため、導入が容易ですぐに運用を開始できます。
初期投資が比較的少なく運用コストも抑えられるため、小規模な倉庫や1フロア型の倉庫に適しています。
オンプレミス型
オンプレミス型は、自社のサーバーと複数の端末で構成されるシステムです。他システムとの連携が容易で、データ共有や管理が効率的に行える特徴があります。
自社のサーバー上で管理できるため、セキュリティーやプライバシーの観点でも安心です。しかし、導入する際は、サーバーやネットワーク機器の購入、設置、構築が必要になり、初期費用や運用コストが高くなる傾向があります。
オンプレミス型は、高い初期投資と運用管理の柔軟性が求められるため、中規模から大規模な倉庫に向いています。
クラウド型
クラウド型は、インターネットを介してクラウド上で運用されるシステムです。初期投資が比較的少なく、短期間で導入できる点がメリットです。拠点間の在庫情報がリアルタイムで更新されるため、作業者は最新の情報に基いてピッキングを行うことが可能です。
ただし、インターネット環境への依存度が高いため、ネットワーク障害の影響を受けやすい点に注意が必要です。
クラウド型は倉庫間でリアルタイムに情報共有できるため、倉庫が複数の拠点に分散している場合におすすめです。
ピッキングデバイスの種類
デジタルピッキングシステムには、主に以下の3つの種類があります。
- 無線式・有線式デジタルピッキング表示器
- スマートフォン・タブレットピッキングシステム
- ボイスピッキングシステム
3つのピッキングデバイスの特徴を詳しく解説します。
有線式・無線式デジタルピッキング表示器
デジタルピッキングには、有線式と無線式があります。これらの表示器は、物流センターや工場などで広く活用されています。
有線式と無線式の違いについて見てみましょう。
有線式デジタルピッキング表示器の特徴
有線式のデジタルピッキングシステムは、配線を通じてデジタル表示器とコントロールユニットを接続します。有線のため、充電不要で長時間の稼働が可能です。
無線式に比べて信号干渉の影響を受けにくく、通信が安定しています。そのため、大規模なピッキングエリアを設計する場合や、固定式のピッキング棚、フローラック、パイプラックを設置する場合に適しています。
ただし、導入時やロケーション変更時に配線工事が必要となるため、倉庫のレイアウトが頻繁に変更される倉庫には不向きなシステムといえるでしょう。
無線式デジタルピッキング表示器の特徴
無線式のデジタルピッキングシステムは、配線工事が不要で自由に設置できます。導入時の手間が大幅に軽減し、柔軟なレイアウト変更にも対応できる点が特徴です。
無線式はバッテリーで動作するため、定期的な充電が必要ですが、充電機能付きの稼働式ラックを使用することで、長時間の稼働も可能です。
従来の通信距離は3.5m程度でしたが、現在では電波干渉を避ける技術が進化し最長30m程度の通信にも対応できます。これにより、工場内アンテナの数を大幅に削減し、効率的な運用が実現しています。
さらに、AGV(製造現場などで材料・工作物・部品・工具などを積み、所定の場所に運ぶ移動ロボット)やAMR(自律走行搬送ロボット・協働型搬送ロボット)などへの搭載もできるため、柔軟な運用を求める企業におすすめです。
スマートフォン・タブレットピッキングシステム
スマートフォン・タブレットピッキングシステムは、専用ハンディターミナルの代わりにスマートフォンやタブレットと連携できるシステムです。
主な機能は下記の通りです。
- シングル/マルチピッキング双方に対応
- 在庫検索機能(出荷期限や在庫数の確認、あいまい検索など)
- 棚卸機能、棚卸進捗の一覧表示
- 在庫検索
- 出荷検品機能(バーコード検品、商品情報の視認性向上、差異対応、商品追加・削除など)
- ロット・期限管理に対応
スマートフォン・タブレットピッキングシステムには、以下のような多くのメリットがあります。
- 低コストで導入できる
- 待機時間を削減できる
- 作業コストを削減できる(作業効率化・ペーパーレス)
- 視認性と操作性が高く、初心者やパートを即戦力化できる
- 誤出荷防止、物流品質を向上させることができる
- 作業進捗や履歴をリアルタイムで確認できる
- 在庫管理システムとのデータ連携によって業務を一元管理できる
操作が簡単でリアルタイムで指示を受け取れるため、多品種少量のピッキング作業に適しています。
初期投資を抑えつつ、操作性の高いデバイスを活用したい企業におすすめです。
ボイスピッキングシステム
ボイスピッキングシステムは、倉庫作業員がヘッドセットを装着し、音声によってピッキング指示を出すシステムです。
ボイスピッキングシステムのメリットは、下記の通りです。
ハンズフリー(両手が自由に使える)
ボイスピッキングシステムは手に機器を持つ必要がなくハンズフリーで作業ができるため、ケース商品や重量物、バラ商品も両手でかつ安全に取り扱うことが可能です。
アイズフリー(視認の必要がない)
ボイスピッキングシステムはアイズフリーでの作業が可能です。視線そらすことなく対象物に集中でき、走行中の音声指示や入力も可能なため、作業効率が大幅に向上します。
作業手順を平準化できる
作業手順を平準化することでスピードが向上し、作業レベルの均一化が図れます。その結果、誰でも同じ作業手順に従って作業ができるようになります。
また、文字ではなく音声で指示を受けるため、外国人や高齢者、障がい者などにも負担なく利用可能です。
読み合わせ作業を廃止できる
読み合わせ作業を廃止できるため、ピッキングや入荷検品、出荷検品、点検検査などの工程で、ピッキングリストと現品の照合を一人で行うことが可能です。
クラウドサービスが利用できる
クラウドサービスを活用することで、システム導入が簡単にになり、初期費用も削減できます。
また、導入後のシステム維持管理も簡単です。
例えば、お菓子メーカーではボイスピッキングを導入し、ピッキング作業の作業効率が26%向上、開梱作業を伴うピッキング作業も15%改善した事例もあります。
さらに、乳製品を扱う企業では、冷凍庫内にボイスピッキングシステムを導入し、作業時間の短縮やハンズフリーによる効率化を実現しています。
デジタルピッキングシステム選定のポイント
デジタルピッキングシステムにはさまざまな種類がありますが、ここでは選定する際のポイントを紹介します。
以下のポイントを考慮しながら選定することをおすすめします。
- 取り扱う商品の特性や作業環境に適しているか
- 費用対効果が十分か
- 操作性はシンプルか
- 既存システムと連携が可能か
- サポート体制は整っているか
取り扱う商品の特性や作業環境に適しているか
デジタルピッキングシステムは、商品の特性や作業環境に適したものを選定しましょう。
例えば、冷凍庫内に設置する場合は、低温環境に対応した機器が必要です。
また、重量物には、ピッキングカートや台車と連携ができるシステム、軽量品や多品種少量の場合は、ハンディ端末を活用した方式が効率的です。
ボイスピッキングシステムなら、手がふさがっている場合でも操作が可能なため、特に動きが多い作業環境に適しています。
システムの使用はメーカーによって異なるため、導入事例なども参考にしましょう。
費用対効果が十分か
デジタルピッキングを導入する際は、以下のような費用がかかります。
- 設置工事費
- システム連携費
- 維持費
そのため、費用対効果が十分に検討した上で選ぶことが重要です。
特に小規模な倉庫では、コストが見合わない可能性もあるため注意が必要です。
デジタルピッキングシステムの使用範囲を明確にし、入出庫頻度の高い商品に限定にするなど、目的に応じた導入を検討しましょう。
操作性はシンプルか
操作性がシンプルな機器かどうかも重要なポイントの一つです。操作性が複雑な機器は、作業員が慣れるまでに時間がかかり、かえって効率が下がる可能性があります。
そのため、システムが直感的で使いやすいか、新人でもスムーズに操作できるかを評価することが大切です。
実際にデモやトライアルでシステムを試用し、現場作業員が使いやすいと感じるかを確認しましょう。
既存システムと連携が可能か
導入済みの既存システムとスムーズに連携できるかも確認しましょう。
デジタルピッキングシステムにもよっては、以下のようなシステムとの連携が可能です。
- 倉庫管理システム(WMS)
- 基幹システム(ERP)
- 輸送管理システム(TMS)
既存システムとの連携により、ピッキングの作業効率や精度をさらに高められます。
サポート体制は整っているか
サポートの範囲や応答時間など、サポート体制を事前に把握しておくことも重要です。
例えば、以下の点を確認しておくと安心です。
- システムの初期設定や設置を行ってくれるか
- 現場スタッフにトレーニングしてもらえるか
- ヘルプデスクが24時間365日対応か
- 保守サービスは夜間や土日も受け付けているか
- システムトラブル時に迅速かつ適切なサポートを提供できる体制が整っているか
導入時やトラブル発生時の対応のほか、必要であればスタッフへのトレーニングの有無も確認しましょう。
デジタルピッキングシステムの導入までの流れ
デジタルピッキングシステムを導入する際の流れは、下記の通りです。
- 業務の現状分析と要件定義
- ベンダー・システムの選定
- 小規模システム(プロトタイプ)でテスト運用
- 本格運用と作業員のトレーニング
- 導入後の運用とメンテナンス
規模にもよりますが、システム導入のキックオフから本稼働まで約3~4ヵ月で導入することが可能です。
導入の流れを、順に解説します。
1. 業務の現状分析と要件定義
倉庫や工場の業務フローを詳細に調査し、紙伝票管理や人的ミス、作業効率の低下など現場の課題を洗い出します。
改善ポイントを特定し、現場作業の全体像を把握します。
2. ベンダー・システムの選定
経営目標とシステム導入目的を明確にし、必要な機能をリストアップします。
該当する機能を搭載しているシステムを複数ピックアップしましょう。
ピックアップしたシステムの提供会社を調査し、提案依頼書(RFP)を活用した情報収集を行います。
RFPとは、要件・目的・評価基準などを明確に記載し、複数のシステム提供会社に提示する文書のことです。自社が求めることを明確に示せるため、すり合わせがスムーズに行えます。
収集した情報や提供情報、システムデモを基に、性能・コスト・サポートを評価してベンダーとシステムを選定しましょう。
3. 小規模システム(プロトタイプ)でテスト運用
選定したシステムを、実際の作業環境でテスト運用し、システムの有効性を確認します。初期テスト結果を基に本格導入を進めて全体展開し、ダウンタイム(システム導入や切り替え作業中に業務が一時的に停止・中断する時間)管理を計画します。
4. 本格導入と作業スタッフのトレーニング
デジタルピッキングシステムの本格導入にあたっては、現場の作業フローに合わせたシステムの最終調整と、作業スタッフに向けた研修の実施が重要です。
新しい仕組みにスムーズに適応できるよう、ピッキング作業の流れや端末の操作方法などを丁寧にレクチャーしましょう。
現場での混乱を防ぐため、マニュアルや動画などを用意し、教育期間を設けて段階的に運用を開始するのが理想的です。
システム導入直後はトラブルが起こりやすいため、ベンダーとの連携を密にしながらサポート体制を整えることも成功の鍵となります。
5. 導入後の運用とメンテナンス
導入後は、ハードウェア・ソフトウェアの定期点検やアップデートを実施し、システムの安定稼働を維持します。
トラブル発生時には前述したように、「事業を止めないための計画(BCP)」を立案し、事業運営できる体制を整えておくことが大切です。
また、定期的にシステムの導入効果を数値化・測定し、システムの改善ポイントを特定しましょう。
おすすめのデジタルピッキングシステム3選
最後に、おすすめのデジタルピッキングシステムを3つご紹介します。
ピッキング Pシリーズ(ギークプラス)
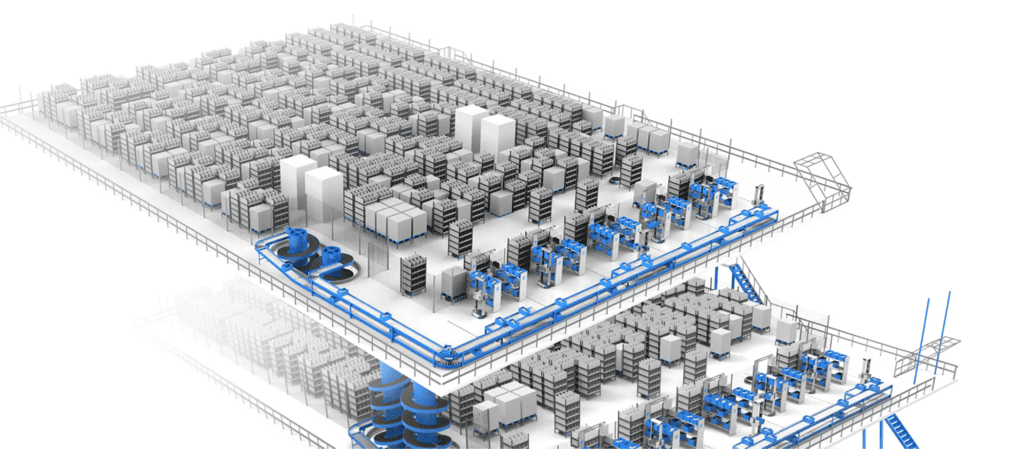
ギークプラスのピッキング Pシリーズは、物流倉庫のピッキング作業を自動化・効率化するロボットソリューションです。
Goods to Person(GTP)方式で、ロボットが在庫棚やコンテナをピッキングステーションまで自動搬送するため、作業員は移動する必要がありません。そのため、正確性・作業効率が大幅に向上し、人的ミスや作業負担を削減できます。
Bin to Person(BTP)ピッキング方式にも対応しており、高密度保管エリアからRoboShuttle™がコンテナを運ぶBTP方式も選択できます。保管効率とピッキング効率を両立し、スペースの有効活用が可能です。
また、走行ロボット(PopPick)は「吸着盤」を採用しており、極限までコンテナの隙間を縮小できるため、在庫保管密度を高められます。
24時間365日の保守サービスも充実しており、世界で10,000台以上の運用実績に関するデータベースを基にした盤石なサポートを提供しているため、導入後の運用も安心です。
ピッキング Pシリーズがおすすめの事業者
- 作業スタッフによってピッキング精度やスピードにバラつきがあるため、業務品質の標準化やミスの削減をしたい事業者
- 倉庫スペースが手狭で、高密度保管や省スペース運用を実現したい事業者
- ピッキング対象が多品種・多頻度で、従来の人手作業では処理能力が限界に達している事業者
詳細情報
企業名 | 株式会社ギークプラス |
所在地 | 東京都渋谷区恵比寿4-20-3 恵比寿ガーデンプレイスタワー 26階 |
ホームページ | https://www.geekplus.jp/ |
digipica(アトムエンジニアリング)
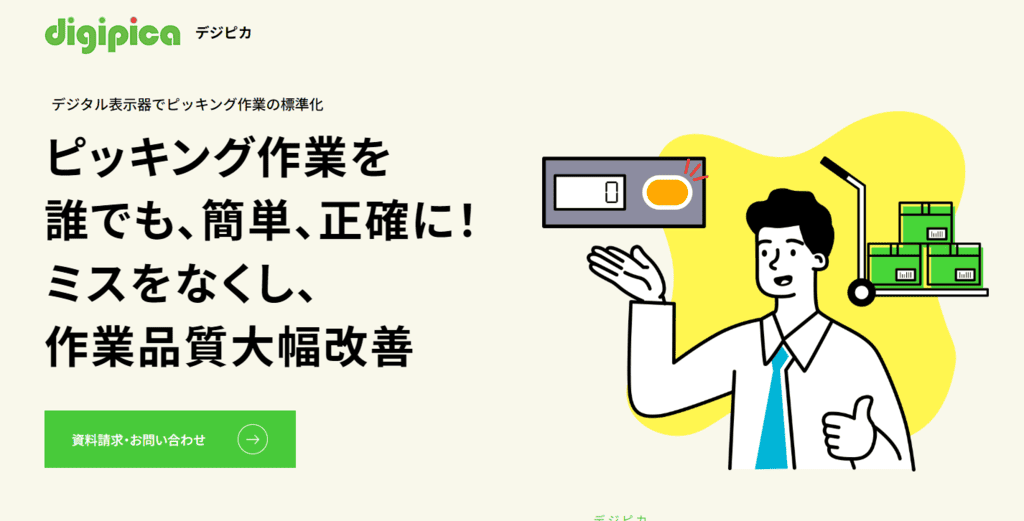
デジピカは、「摘み取り方式(注文ごとにピッキングを行う方法)」のピッキング作業に対応しているシステムです。
設置した表示器のランプが点灯し、デジタル画面にピッキング数量が表示されるため、作業者は「光った棚から指定数の商品を取る」だけでピッキングが完了します。そのため、商品知識がない初心者やパート・アルバイトでも即戦力化できるシンプルな設計となっています。
有線表示器と無線表示器を併用でき、現場に合わせた柔軟な運用も可能です。
出荷頻度が高い商品の間口に表示器を設置し、ハンディターミナルと併用することで導入コストを抑えられます。
digipicaがおすすめの事業者
- 初心者にも簡単・正確にピッキング作業を行わせたい事業者
- 商品の種類が多く、オーダーごとの出荷量が少ない事業者
- 急な出荷指示やレイアウト変更にも、柔軟に対応できるシステムが必要な事業者
詳細情報
企業名 | 株式会社アトムエンジニアリング |
所在地 | 栃木県宇都宮市御幸ケ原町10-44 |
ホームページ | https://www.atm-net.co.jp/pro/digipica/ |
部品の達人(アイオイ・システム)
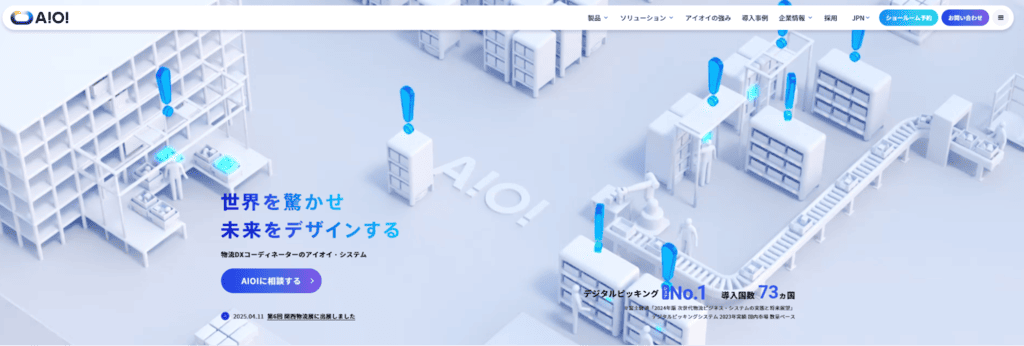
部品の達人は、デジタル表示器やシグナルライトを活用した効率的・高精度なピッキングを可能にするシステムです。
ソフトの初期設定はシンプルで、導入後も設定変更や修正作業も容易に行えるため、すぐに運用を開始できます。
以下のように、現場の運用に合わせた多様な作業形態に対応できるのが特徴です。
- 複数エリア
- 複数人での同時並行作業
- 順立て(指示順序通りのピッキング)
- セル生産方式
- ブロックリレー(エリアごとのリレー方式)
- マルチワーク(複数人同時作業)
さらに、オプション機能としてピッキング場所の間違いを防止する「ポカよけ機能」を搭載しています。詳細作業ログの出力も可能なため、業務分析や改善にも活用できます。
部品の達人がおすすめの事業者
- ピッキング作業を標準化したい事業者
- 類似部品や品種が多く、取り間違い・数量ミスが発生しやすい事業者
- 作業進捗や履歴を可視化し、現場改善や人員配置の最適化に活かしたい事業者
詳細情報
企業名 | 株式会社アイオイ・システム |
所在地 | 東京都品川区南大井6丁目22-7 大森ベルポートE館 9階 |
ホームページ | https://www.hello-aioi.com/ |
まとめ:ピッキングにおける課題を解決しながら、費用対効果の向上も追求しよう
本記事では、デジタルピッキングシステムの基礎知識やシステムの選定方法、おすすめのシステムについて解説しました。
デジタルピッキングシステムを導入することで、作業の正確性と効率が向上し、初心者でもスムーズにピッキング業務ができるようになり、人的ミスも大幅に削減できます。
一方で、システム導入や運用にはコストがかかるため、商品の特性や作業環境に適したシステムを選ぶ必要があります。
ピッキング業務の課題を解決しつつ、費用対効果の向上を図るには、現場のニーズに合った機能を見極め、無理のない範囲で導入を進めることが重要です。
デジタルピッキングシステムを選ぶ際は、本記事で解説した導入形態・デバイスの種類・導入までの流れをぜひ参考にしてください。